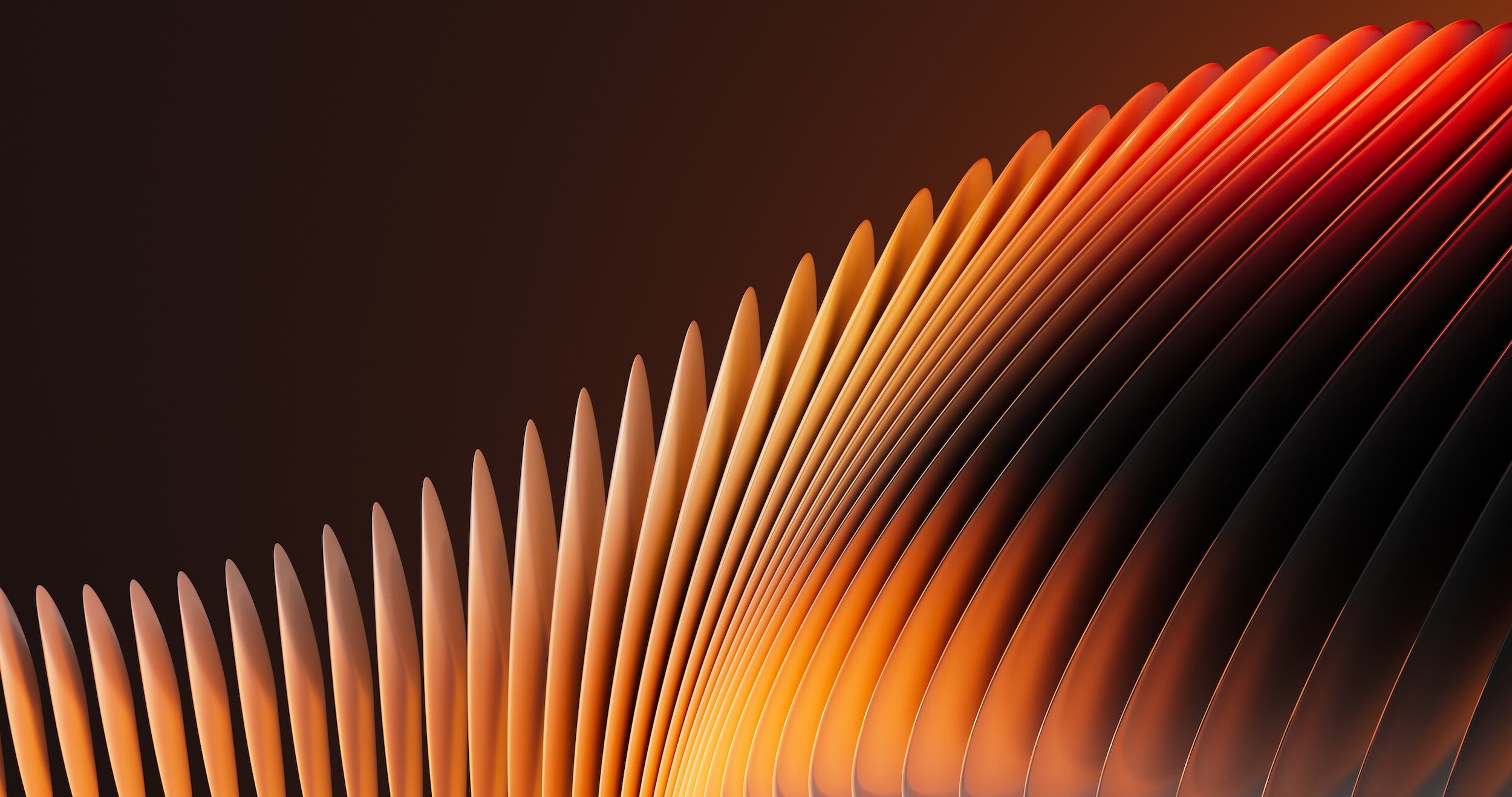
Markets
AEROSPACE & DEFENSE
This market segment includes aerospace and defense applications using Molybdenum, Tungsten, and Tantalum metal products and their alloys. The range of customers varies with each product, as does the compexity of the parts.
Isothermal Forging Dies
Molybdenum alloys TZM, MoLa, and MHC can withstand high temperatures and wear and are thus used for dies in the isothermal forging of super alloys. Aero and land based turbines can be made through the isothermal forging of super alloys into shapes. In order to improve the flow characteristics of the super alloy material, the die needs to be heated to the starting work piece temperature. This also facilitates the forging process because it eliminates cooling at the interface.
Molybdenum Isothermal forging dies are manufactured from Molybdenum alloys – Titanium Molybdenum Zirconium (TZM), Molybdenum Lanthanum (MoLa) or Molybdenum Hafnium carbide (MHC).
Missile Components
Missile rocket motor components can be made using molybdenum because it can resist high temperatures (directional vanes, and rocket nozzles). Tungsten alloy is also used in gyroscopes on missile navigation systems.
Aircraft Balance Weights
To make Tungsten heavy alloy components, WHA powder is blended, pressed, and sintered into a net shape part and then final machined to finish dimension. Near Net Shape Tungsten Heavy Alloy (WHA) provides density and strength, can balance and stabilize control surfaces of ailerons, elevators, aircraft rudders, and helicopter rotor blades and seating. In order to reduce vibration and to enhance pilot and passenger comfort, fixed and rotary wing aircrafts must have precision balancing, which can be provided by materials that are produced for the optimum weight concentration.
Ordinance
Due to it’s strength, wrought tungsten alloys are suitable for long rod penetrators (which are hyper-velocity, armor-penetrating rods in anti tank missiles and shells). They can also be used in fragmentation devices and certain techniques also allows the material to improve elongation or tensile strength. The long rod penetrators are also rotary forged to improve tensile properties.
Security Screening
The leading technologies for security screening at port, airport, and building sites are x-ray and backscatter, both of which can use WHA collimation and shielding systems to improve resolution and performance. These items can also be exported to the medical market but the market in security screening continues to grow.
Single crystal Sapphire’s properties as an electrical insulator while providing high heat conductivity makes it an excellent substrate for high heat generating electrical circuits such as Light Emitting Diodes and high power integrated circuits as found in satellite and other high frequency communication technologies. For the production of LED’s, Sapphire wafers are used as a non-conducting substrate for the growth of devices based on Gallium Nitride (GaN). Sapphire crystals also have uses other than as LED substrates, for example sighting windows on missile and missile guidance hardware, furnace sight windows, and watch glass.
There are a number of ways to make Sapphire crystals. For the LED market, the most popular are the Kryopolous and Czochralski techniques. Wafers are cut from an ingot which is produced by melting high-purity Alumina in a Tungsten or Molybdenum crucible within a vacuum furnace using either a Molybdenum or Tungsten hot zone. A precisely oriented rod-mounted seed crystal is dipped into the molten Alumina. The seed crystal’ʹs rod is slowly pulled upwards and rotated simultaneously. By precisely controlling the temperature gradients, rate of pulling and speed of rotation, it is possible to extract a large, single-crystal, cylindrical ingot from the melt.
Other methods exist, including edge-defined film-fed growth (EFG), heat-exchanger method (HEM), and vertical‑horizontal gradient freezing (VHFG). The method of growth determines the type and form of refractory metal used.
Sapphire melting furnace hot zones are manufactured from thin‑gauge Molybdenum or Tungsten and formed into a cylindrical heat shield around the crucible. These shields are similar to those used in vacuum-furnace heat shields, except that their operating temperature and environment are more aggressive. The crucibles are either spun from Molybdenum or Tungsten sheet to produce a thin wall crucible or fabricated from either Molybdenum or Tungsten using CIP and sinter technology depending on the furnace design.
SAPPHIRE
ELECTRONIC
Refractory metals can be used in a number of ways in the electronics market. Ion Implantation, Physical Vapor Deposition (PVD), Metalorganic Chemical Vapor Deposition (MOCVD) and Molecular Beam Epitaxy (MBE) are just some of the semiconductor manufacturing applications that can use precision-machined parts in either assembled or part forms.
Ion Implantation
Ion implantation is the injection of the ion beam with an energy order of 100keV into a material where the ion beam will have a series of physical and chemical interactions with atoms or molecules in the material. The incident ions gradually lose their energy, and finally stop in the material and cause a change in composition, structure and properties of the surface of the material, thus optimizing the surface properties of the material, or giving some new excellent performance to the material.
Evaporation deposition (PVD)
A form of physical vapor deposition (PVD) called evaporation deposition is used to deposit thin films onto substrates through the evaporation of the film material and further condensation of the vapor onto said substrate, usually thin films on small substrates. The deposition of aluminum on semiconductor wafers is extremely efficient and doesn’t risk damaging the substrate. Other uses include depositing aluminized film for balloons, snack bags, and the coating of cutting tools in metalworking.
The process proceeds as follows: In a vacuum chamber, film material is stored in small boats and heated to a point where the material vaporizes. The resulting vapor is then mixed with a gas to form a compound which is then condensed onto the substrate as a highly adherent coating. During the process, molybdenum boats are used because they can withstand the heat needed to vaporize the pure metals and corrosion from the resulting gaseous compounds.
Metal Organic Chemical Vapor Deposition (MOCVD) and Molecular Beam Epitaxy (MBE)
To grow crystalline layers on substrates for compound semiconductors multilayer structures, MOCVD and MBE chemical vapor deposition methods can be used to deposit solid films of complex organometallic compounds such as GaAs, GaN, AlGaAs, AlGaInP and InGaN on sapphire wafers. MOCVD occurs in gas phase at pressures of 2-100 kPa while MBE travels through a vacuum of 10-8 PA before condensing on the substrate. These methods are now used in major manufacturing processes for LED semiconductors, cell phone transistors, and WiFi and solar cells.
The heated gas of individual compounds is mixed with heated gas and then deposits onto the substrate. The excess gas is exhausted out of the chamber and liquidized for disposal. In the chemically aggressive gallium arsenide (GaAs) environment of MOCVD reactors, molybdenum is most useful due to it’s high temperature tolerance and relative nobility.
Some products include exhaust rings, wafer support trays, attachments, and evaporation boats for specialist wafer coatings. Of these products, wafer support trays, which are manufactured from 1.5-3.0 mm sheets, have the largest volume. Since these carrier are present in the deposition chambers and exposed to the chemicals and temperatures, they are a consumable item.
SPUTTERING
Physical Vapor Deposition ( PVD ) is a method to deposit thin layers of a desired material onto a substrate.. The process consists of a magnetron to dissociate atoms, from a source or “target” onto a substrate, such as silicon wafers or glass. This can be used in thin anti-reflection coatings on glass for optical applications, the production of thin film transistors, or nitriding of tools. Sputtering is most useful when (a) there is a large area of deposition (b) when the thin film is from a high temperature material that cannot be deposited through evaporation or (c) when it is necessary to keep the substrate at low temperatures or (d) when a thin atomic layer is required.
Thin film transistor liquid crystal display (TFT LC)
Thin film transistors (TFT) are used to control the color of light (red, blue, or green) in each pixel of flat panel displays. Image quality on television sets, computer monitors, mobile phones, handheld video game systems, navigation systems and any other devices utilizing screens is greatly improved.
Often TFT technology requires Molybdenum or Molybdenum alloys to be a barrier between the transistors and glass substrates. It provides a stable layer, which has a good adhesion to glass, onto which to deposit the conductive layer, while protecting the circuitry from subsequent etching processes. The purity of the Molybdenum will tell how effective the bond to the glass substrate is and the evenness of the coating. Any impurities within will cause splashing and an uneven coating.
A magnetron sputtering process deposits the Molybdenum coating which induces plasma ions of a gas to bombard a Molybdenum target. Then the surface atoms of the target material are deposited onto the surface of the substrate. The most common form of target is the planar disc or rectangle (although rotary tubes are also used) bonded to a Copper backing plate.
Although the size of the plate depends on the size of the substrate to be coated, there is a push towards larger plates in order to improve the cost/area for TFT LCD production.
Organic LED Technologies
OLEDs are used in the same consumer electronic applications as TFT LCD FPD but they do not require backlighting panels. Therefore they offer improved energy usage and are thinner and lighter. For higher resolution and larger displays, many OLEDs use a thin film transistor backplane to switch each individual pixel on or off, similar to TFT LCD technology.
OLEDs contain a very thin (250 nm) layer of Molybdenum Aluminum, which is on a glass substrate and is used as a buffer layer to the Indium Tin Oxide electrode material. This layer improves reflectivity and is much thinner than that used in TFT LCD technologies. Although it is expected that the growth and commercialization of OLED displays will use more of Molybdenum, this may not increase the tonnage because of the reduced sputtering thickness.
Solar
Photovoltaic technologies used in capturing energy from sunlight in solar panels have focused on the cost per kw energy produced as well as the increasing efficiency gained from the production of energy from daylight rather than direct sunlight. As Silicon prices rise to the demand of the solar industry, two type of thin film technologies have become commercially available; both of which utilize Molybdenum.
Copper Indium Gallium Selenide (CIGS) PV Technology
CIGS is a semiconductor material can be used for the manufacturing of solar cells because the material is strongly absorbent to sunlight. This results in less material than silicon based technologies, which reduces the cost while maintaining efficiency. In a CIGS solar cell, the CIGS absorber material is deposited onto a thin film of Molybdenum which is attached via sputtering to a glass substrate. The Molybdenum serves as both the back electrical contact and is used to reflect any unabsorbed light back to the absorbing layer.
Cadmium Telluride (CdTe) PV Technology
CdTe technology was developed as a lower cost alternative to Crystalline Silicon. It uses Cadmium Telluride semiconductor material to absorb light. CdTe enables high-volume, low-cost production of solar modules in a continuous, automated process that uses less semiconductor materials. Molybdenum is used as the metal buffer layer because it is chemically compatible with the CdTe material and is extremely stable. It is deposited as a thin film via sputtering.
GLASS
The production of glass is a global business that has manufacturing sites in most countries around the world. The industry itself is split into four type of products: fiber, container, quartz and float glass.The process of production for all four types require high temperatures in a corrosive environment. Thus, Molybdenum and Tungsten make the most stable furnaces electrodes and melting architecture due to their corrosion resistance and thermal stablity. For container glass and glass fibre production molybdenum glass melting electrodes are used, there are other uses such as furnace liners, hearth plates, and stirrers.
Glass Melting Electrodes (GME’s)
The bars are threaded and joined together to be pushed into the furnace. The electrodes are either mounted on the top, side, or bottom depending on the type of furnace. However top mounted electrodes wear much quicker due to oxidation, and sometimes require coating. Since Molybdenum is extremely stable at high temperatures and is resistant to corrosion, they are the material of choice for container glass and fiber glass manufacturing. We are able to offer coating and specialist alloys for longevity and improved performance.
Quartz Melting Furnace parts
In high temperature and optically pure applications, fused quartz is required. They are used most often as the envelope in Halogen lamps, heating elements, and large diameter furnace tubes for semiconductors because they are able to withstand high temperatures. In order to make fused quartz, you must fill a crucible with quartz stand and melt it at 2000 °C. The result is then taken through an orifice plate to either form rods, plates, or through a mandrel to make tubes. Since Tungsten can withstand high temperatures, they are used for drawing components, heating elements, forging mandrel shafts, and making crucibles.
Glass Melting Tank Shielding
Large glass melting tanks can hold up to 1000 MT and are used in volume glass production, Refractory bricks line the melt tank as the insulating surface but depending on the glass type and furnace design, the brick material may be corroded by the chemical reactions during the process. To combat this, the melt tanks are sometimes equipped with molybdenum, especially in areas of high flow. This will improve the longevity of the furnace while also avoiding high costs in the future.
The most popular uses of refractory metals in the medical market is in X-ray generation or radiation shielding applications. Over the last decade, there has been a move towards improved diagnosis and treatment therapies, which has led to more sophisticated equipment that require more complex refractory metal components. The majority of the uses of refractory metals in this market require precision machining, assembly, forming and forging.
Isotope Shielding
In nuclear medicine radioactive isotopes are used in the diagnosis and treatment of patients. In this procedure, radioactive isotopes are administered to the patient and then imaged using radiation detectors. These images can be specifically localized to various organs or cellular receptors and can show the extent of a disease in the body based on the cellular function and physiology.
Nuclear medicine imaging studies is generally more organ and tissue specific (e.g.: lungs scan, heart scan, bone scan, brain scan, etc.) than those in conventional radiology imaging, which focuses on a particular section of the body (e.g.: chest X-ray, abdomen/pelvis CT scan, head CT scan, etc.).
Radioactive isotopes are delivered to the patient through Tungsten containers and shielded syringes in order to not expose the clinician. When a radioactive isotope is used as a source of radiation, isotope shielding containers are used in Radiotherapy equipment. Large 400 x 400 x 400 mm WHA containers are used to shield the rest of the equipment from the radiation and is the source for transportation and exchange.
X-ray Technologies
Refractory metals have been used to generate x-rays for many years using Molybdenum and Tungsten anodes. As the images become more sophisticated with 3D imaging via Computer Tomography (CT), there is a push for more complex materials and components, many of which require high power rotating anodes and sophisticated collimation units. Medical equipment such as CT Scanners use rotating x-ray anodes. Th9s is a complex part containing the rotating anode, shaft, bearings, and susceptor cup. It is then enclosed in a glass vacuum sealed case.
Radiation Therapy Equipment
These medical devices deliver a controlled dose of radiation generated by a linear accelerator or LINAC. Tungsten heavy alloy is used extensively to both shield the operator and patient from radiation, and to deliver the exact dose to the cancerous cells. The delivery is controlled using a multi-leaf collimator of MLC. This is manufactured using tungsten heavy alloy.